Восстановление деталей с помощью лазерной наплавки. Современное решение для продления срока службы деталей
Восстановление деталей с помощью лазерной наплавки. Современное решение для продления срока службы деталей
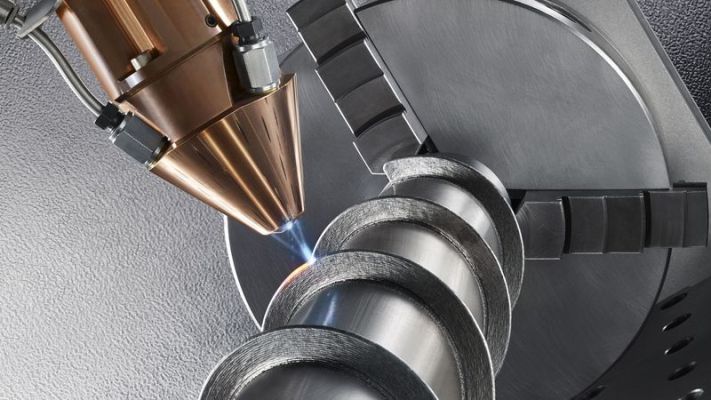
- Что такое лазерная наплавка?
- Принцип работы лазерной наплавки
- Типы лазеров, используемых при лазерной наплавке
- Непрерывная и импульсная наплавка
- Материалы, используемые при лазерной наплавке
- Функции лазерной наплавки
- Подготовка подложки
- Области применения лазерной наплавки
- Этапы лазерной наплавки
- Преимущества наплавки лазером
- Недостатки технологии
- Сравнение лазерной наплавки с традиционными методами
- Лазерная наплавка по сравнению с термическим напылением
- Лазерная наплавка по сравнению с гальваническим покрытием
- Лазерная наплавка по сравнению со сваркой
- Сравнительная таблица
- Ответы на часто задаваемые вопросы
Когда дело доходит до производства и ремонта, существуют различные методы и технологии, которые могут помочь создать высококачественную продукцию с повышенной прочностью и функциональностью. Одной из таких технологий является лазерная наплавка. Но что такое лазерная наплавка? Проще говоря, это процесс нанесения слоя материала на подложку с помощью лазерной технологии.
Умело сочетая высокую точность с универсальностью применения, она быстро завоевала популярность во многих отраслях промышленности. В этой статье мы погрузимся в сложный, но увлекательный процесс лазерной наплавки, рассмотрим принцип работы, сферы применения и преимущества данной технологии.
Что такое лазерная наплавка?
Лазерная наплавка - это метод модификации поверхности с помощью наплавления слоя материала на подложку. Это одна из форм аддитивного производства, в которой используется лазерная технология для нанесения материала на поверхность подложки. Процесс включает использование лазерного луча, который направляется на поверхность, создавая расплавленный бассейн. Затем порошковый материал вводится в этот бассейн, где он плавится и застывает, образуя металлургическую связь с подложкой. Процесс можно повторить несколько раз, чтобы создать несколько слоев, образуя толстое покрытие. Наплавка выполняется с помощью станков, оснащенных лазерными генераторами диодного, алюмоиттриевого или оптоволоконного типа.
Рис. 1. Высокоскоростная лазерная наплавка
Принцип работы лазерной наплавки
Лазерная наплавка включает в себя нанесение металлического порошка или проволоки на материал подложки, который сплавляется с помощью мощного лазерного луча. Этот сложный обмен между лазером и подложкой создает металлургическое соединение металлов, которое отличается улучшенными свойствами, такими как повышенная износостойкость и устойчивость к коррозии. Метод лазерной наплавки позволяет точно и целенаправленно наносить материалы на нижележащий субстрат с ограниченным тепловложением.
Лазерная наплавка металла делается с помощью порошковых, газопорошковых присадок и проволоки. Существуют разные способы подачи расходного материала:
- коаксиальная;
- латеральная;
- радиальная.
Рис. 2. Принцип работы лазерной наплавки
Типы лазеров, используемых при лазерной наплавке
Для лазерной наплавки обычно используются мощные лазеры, способные обеспечить необходимую плотность энергии для эффективного расплавления и осаждения материала наплавки. Наиболее распространенными типами лазеров, используемых для лазерной наплавки, являются:
CO2-лазеры
CO2-лазеры - это газовые лазеры, которые производят непрерывное излучение на длине волны 10,6 микрометров в инфракрасном диапазоне. Они обладают высокой мощностью - от нескольких сотен ватт до десятков киловатт. CO2-лазеры широко используются для различных промышленных применений, включая лазерную наплавку, благодаря своей высокой эффективности, отличному качеству луча и относительно низкой стоимости.
Nd:YAG лазеры
Лазеры на иттрий-алюминиевом гранате, легированном неодимом (Nd:YAG), - это твердотельные лазеры, излучающие свет с длиной волны 1,064 микрометра в ближнем инфракрасном диапазоне. Nd:YAG-лазеры могут работать в непрерывном или импульсном режиме, что обеспечивает гибкость для различных применений лазерной наплавки. Они имеют хорошее качество луча, легко фокусируются и передаются по оптическому волокну.
Волоконные лазеры
Волоконные лазеры - это тип твердотельных лазеров, в которых активной средой усиления является оптическое волокно, легированное редкоземельными элементами, такими как эрбий, иттербий или неодим. Волоконные лазеры производят высококачественное излучение в ближней инфракрасной области, обычно около 1,07 микрометра. Они обеспечивают высокие уровни мощности, отличное качество луча и хорошую энергоэффективность. Преимуществом волоконных лазеров также является легкая интеграция с роботизированными системами и возможность передачи лазерного луча через гибкое оптическое волокно, что делает их все более популярным выбором для лазерной наплавки.
Выбор лазера для конкретного применения лазерной наплавки зависит от таких факторов, как требуемый уровень мощности, качество луча, длина волны, параметры процесса и общая стоимость системы. По мере развития технологии новые типы лазеров и усовершенствование существующих лазерных систем будут продолжать расширять возможности и области применения лазерной наплавки.
Непрерывная и импульсная наплавка
Непрерывная и импульсная лазерная наплавка - это два различных режима работы, используемых в процессах лазерной наплавки. Каждый режим имеет свои преимущества, в зависимости от требований и желаемых результатов конкретного процесса наплавки.
При непрерывной лазерной наплавке используется лазер непрерывной волны (CW) для генерации устойчивого, непрерывного пучка энергии. Этот режим обеспечивает постоянное поступление тепла, что позволяет сформировать непрерывный расплав на подложке. При движении лазера вдоль поверхности расплавленный материал застывает, образуя связь с подложкой.
При импульсной лазерной наплавке импульсный лазер используется для генерации серии коротких высокоэнергетических импульсов. Этот режим обеспечивает прерывистый подвод тепла, в результате чего на подложке образуются небольшие, дискретные бассейны расплава. Автоматизированная импульсная наплавка применяется для работы с новыми изделиями. Благодаря минимальному нагреву детали, она существенно снижает склонность наплава к растрескиванию. Материал наплавки подается в эти бассейны расплава, где он сплавляется с подложкой перед застыванием.
Рис. 3. Лазерная наплавка с помощью зеленого лазерного излучения
Материалы, используемые при лазерной наплавке
Материалы, используемые при лазерной наплавке, могут варьироваться в зависимости от области применения и используемой подложки. Некоторые из распространенных материалов, используемых при лазерной наплавке, включают:
- Металлические порошки (никель, кобальт, титан и алюминий);
- Керамические порошки (диоксид циркония, глинозем и карбид кремния);
- Порошки для термического напыления (карбид вольфрама, карбид хрома и керамические покрытия.)
Выбор материала для наплавки зависит от желаемых свойств и требований к применению:
- Нержавеющая сталь: Обладает отличной коррозионной стойкостью и механическими свойствами;
- Сплавы на основе никеля: Обеспечивают высокотемпературную прочность и устойчивость к окислению;
- Сплавы на основе кобальта: Обеспечивают износостойкость и коррозионную стойкость в высокотемпературных средах;
- Карбидные композиты: придают исключительную износостойкость и твердость.
Функции лазерной наплавки
Ремонт и восстановление: Восстановление изношенных или поврежденных компонентов, таких как лопатки турбин, шейки подшипников или детали двигателя.
Защита от износа: Повышение износостойкости деталей, подвергающихся абразивному и коррозионному воздействию.
Коррозионная стойкость: Нанесение антикоррозионных покрытий на детали, подвергающиеся воздействию агрессивных химических веществ или экстремальных погодных условий.
Функциональные поверхности: Создание индивидуальных свойств поверхности, таких как электропроводность или теплоизоляция, путем комбинирования различных материалов.
Подготовка подложки
Процесс лазерной наплавки начинается с подготовки подложки, которая включает в себя очистку и подготовку поверхности для обеспечения надлежащего сцепления. Затем подложка предварительно нагревается до определенной температуры, чтобы облегчить сцепление с добавляемым материалом. Лазерный луч направляется на поверхность подложки, создавая расплавленный бассейн. Затем порошковый материал вводится в бассейн, где он плавится и соединяется с подложкой.
Рис. 4. Процесс лазерной наплавки проволокой
Области применения лазерной наплавки
Наиболее широко наплавка лазером применяется для:
- нефтегазовой промышленности;
- облицовки поверхностей,
- судостроения;
- генерального машиностроения;
- металлургии;
- обработки макроматериалов;
- на предприятиях, выпускающих гипсоцементные составы;
- ремонтной сварки;
- ремонта металлических инструментов, штампов, пресс-форм;
- аэрокосмического производства
- других отраслей промышленности.
Энергетика
В энергетическом секторе лазерная наплавка используется для ремонта и улучшения характеристик важнейших компонентов электростанций, таких как лопатки турбин, паровые клапаны и трубы котлов. Лазерная наплавка особенно полезна в этой отрасли, поскольку с ее помощью можно ремонтировать компоненты, которые в пришлось бы полностью заменить, что значительно экономит время и деньги.
Изготовление инструментов и штампов
Лазерная наплавка также используется в инструментальной и штамповочной промышленности для ремонта и повышения производительности пресс-форм, штампов и пуансонов. Эта технология позволяет производителям быстро восстанавливать изношенную или поврежденную оснастку, что сокращает время простоя и повышает производительность.
Горная промышленность
В горнодобывающей промышленности лазерное армирование используется для ремонта и повышения производительности компонентов тяжелого оборудования, таких как зубья ковша, зубья лопаты и буровые долота. Ремонтируя эти компоненты с помощью лазерной наплавки, производители могут продлить срок их службы и снизить потребность в замене деталей.
Автомобильная промышленность
В автомобильной промышленности лазерная наплавка используется для ремонта и улучшения характеристик компонентов двигателя, таких как поршни, гильзы цилиндров и распределительные валы. Лазерная наплавка также может использоваться для нанесения износостойких покрытий на компоненты двигателя, что помогает продлить срок их службы и улучшить эксплуатационные характеристики. Кроме того, лазерная наплавка используется в производстве высокопроизводительных гоночных компонентов, таких как впускные коллекторы и выпускные коллекторы.
Медицина
В области медицины лазерная наплавка используется для производства высокоточных медицинских имплантатов, таких как искусственные суставы и зубные имплантаты. Лазерная наплавка позволяет производителям изготавливать имплантаты со сложной геометрией и индивидуальными формами, которые соответствуют индивидуальным анатомическим особенностям каждого пациента. Эта технология также позволяет производить имплантаты с улучшенной биосовместимостью, что снижает риск отторжения и улучшает результаты лечения пациентов.
Знаете ли вы, что лазерная наплавка также используется в ювелирной промышленности для создания уникальных рисунков и узоров на драгоценных металлах? Используя сочетание лазерной наплавки и традиционных технологий изготовления ювелирных изделий, ювелиры могут создавать замысловатые узоры, которые невозможно получить традиционными методами.
Этапы лазерной наплавки
Процесс лазерной наплавки состоит из следующих этапов:
- Подготовка. Поверхность подложки очищается и предварительно обрабатывается для обеспечения надлежащего сцепления материала наплавки;
- Напыление материала. Металлический порошок или проволока подается в фокус лазера, где он плавится и образует небольшой расплавленный бассейн на подложке;
- Наплавка. Лазер и механизм подачи материала движутся согласованно, создавая непрерывный слой наплавленного материала;
- Охлаждение. Только что сформированный наплавленный слой охлаждается и застывает, создавая прочное соединение с подложкой;
- Последующая обработка. Наплавленная поверхность может быть обработана и отполирована для достижения желаемого внешнего вида и свойств.
Рис. 5. Порошок для лазерной наплавки
Преимущества наплавки лазером
- Точность. Процесс позволяет точно контролировать толщину, состав и расположение материала наплавки, если лазер правильно откалиброван.
- Низкое тепловыделение. Высокая плотность энергии лазера минимизирует зону термического воздействия, снижая риск деформации и остаточных напряжений.
- Минимальные отходы. Аддитивный характер процесса приводит к снижению расхода материалов и минимальному образованию отходов.
- Высокая прочность соединения. Лазерная наплавка образует связь с подложкой, что приводит к более прочному и долговечному соединению, чем механические связи, образующиеся при термическом напылении или гальваническом покрытии. Это приводит к улучшению эксплуатационных характеристик и долговечности обработанных компонентов.
- Низкий уровень искажения. Высокая плотность энергии лазера обеспечивает небольшую зону термического воздействия, сводя к минимуму разбавление материала. Это снижает риск искажений, сохраняя целостность и стабильность размеров обработанных деталей.
- Высококачественное покрытие. Лазерная наплавка позволяет получать плотные, однородные покрытия с минимальным окислением, по сравнению с другими видами обработки поверхности.
- Гибкость процесса. Возможность контролировать различные физико-химические параметры процесса, такие как мощность лазера, размер пятна и скорость подачи материала, что позволяет оптимизировать процесс наплавки в соответствии с требованиями конкретного применения.
- Уменьшение дополнительной обработки. Высококачественные покрытия, получаемые при лазерной наплавке, требуют минимальной последующей обработки, такой как механическая обработка и полировка, что позволяет сэкономить время и снизить затраты. Кроме того, возможность выборочного нанесения материала там, где это необходимо, приводит к уменьшению отходов материала и более эффективному использованию ресурсов.
Рис. 6. Лазерная наплавка на подложку
Недостатки технологии
Понимание недостатков может помочь в оценке пригодности метода для конкретных сфер и определить области применения данной технологии.
Высокие первоначальные инвестиции и затраты на оборудование
Одним из наиболее существенных недостатков лазерной наплавки являются высокие первоначальные инвестиции, необходимые для приобретения оборудования. Системы лазерной наплавки, состоящие из мощного лазера, систем подачи порошка или проволоки и систем управления движением, могут быть дорогими для приобретения. Кроме того, регулярное техническое обслуживание и замена расходных компонентов могут способствовать увеличению общих эксплуатационных расходов.
Сложность обучения
Лазерная наплавка - сложный процесс, для эксплуатации и обслуживания оборудования могут потребоваться квалифицированные техники и инженеры. Соответствующее обучение и опыт необходимы для обеспечения стабильных результатов, избежание ошибок и предотвращения потенциального повреждения компонентов или оборудования. Постоянное обучение может стать барьером для компаний, желающих внедрить лазерную наплавку в качестве новой технологии.
Ограниченный размер и производительность
Размер сборки и скорость наплавки могут быть ограничены, особенно по сравнению с другими технологиями аддитивного производства или традиционными методами обработки поверхности. Эти ограничения могут повлиять на общую производительность и сделать процесс менее подходящим для крупномасштабного производства, требующего больших площадей покрытия.
Потенциальное растрескивание и пористость
При лазерной наплавке обычно получаются высококачественные, плотные покрытия, однако существует риск образования трещин или пористости, если процесс не контролируется должным образом. Такие факторы, как выбор материала, параметры процесса и скорость охлаждения, могут повлиять на образование дефектов, которые могут поставить под угрозу эксплуатационные характеристики и долговечность обработанных компонентов.
Сравнение лазерной наплавки с традиционными методами
Для сравнения лазерной наплавки с традиционными методами обработки поверхности важно понимать различия в процессе, качестве и общих результатах. Здесь мы подробнее рассмотрим лазерную наплавку в сравнении с некоторыми распространенными методами, такими как термическое напыление, гальваника и сварка.
Срок эксплуатации винтов с лазерным покрытием на 60% больше, чем у таких же изделий с азотированием из высоколегированных сплавов.
Лазерная наплавка по сравнению с термическим напылением
Термическое напыление предполагает нагревание материала покрытия, обычно в виде порошка, до расплавленного или полурасплавленного состояния и нанесение его на подложку с помощью высокоскоростного газового потока. Материал покрытия застывает при ударе, образуя механическую связь с подложкой. В отличие от этого, при лазерной наплавке используется мощный лазер для расплавления материала покрытия, который сплавляется с подложкой, создавая прочную связь.
Основные различия между лазерной наплавкой и термическим напылением включают:
- Прочность соединения: Лазерная наплавка создает более прочное соединение, что приводит к лучшей адгезии, долговечности и устойчивости к расслаиванию по сравнению с механическим соединением, образующимся при термическом напылении.
- Качество покрытия: Лазерная наплавка создает полностью плотные, однородные покрытия с минимальным окислением, обеспечивая высокую износостойкость.
- Потребление тепла: Лазерная наплавка имеет меньшую зону термического воздействия благодаря высокой плотности энергии, что снижает риск искажения и остаточных напряжений в обрабатываемых деталях.
Рис. 7. Плазменное термическое напыление
Лазерная наплавка по сравнению с гальваническим покрытием (хромирование)
Гальваника - это электрохимический процесс, при котором тонкий слой металла наносится на подложку путем погружения ее в раствор, содержащий ионы металла, и подачи электрического тока. В отличие от этого, лазерная наплавка - это процесс аддитивного производства, при котором наносится более толстый и прочный слой материала с помощью лазера, который расплавляет и сплавляет его с подложкой.
Основные различия между лазерной наплавкой и гальваническим покрытием включают:
- Совместимость материалов: Лазерная наплавка совместима с более широким спектром материалов, включая металлы, сплавы и композиты, в то время как гальваника ограничивается только металлами.
- Толщина покрытия: Лазерная наплавка позволяет получать более толстые покрытия с контролем над процессом, что позволяет создавать индивидуальные свойства поверхности и геометрию.
- Воздействие на окружающую среду: Лазерная наплавка более экологична, так как при ней образуется меньше отходов и не используются опасные химикаты и токсичные материалы, обычно связанные с гальваническим покрытием.
Рис. 8. Гальваническое покрытие(хромирование)
Лазерная наплавка по сравнению со сваркой
Сварка - это процесс соединения двух или более металлических деталей путем их сплавления, часто с добавлением присадочного материала. Хотя лазерная наплавка также использует лазер для расплавления материала, ее основной целью является создание поверхностного слоя, а не соединение деталей.
Основные различия между лазерной наплавкой и сваркой включают:
- Применение: Лазерная наплавка направлена на улучшение поверхности или и ремонт деталей, в то время как сварка в основном используется для соединения и сборки деталей.
- Потребление тепла: Лазерная наплавка имеет меньшую тепловую нагрузку и меньшую зону термического влияния, что сводит к минимуму искажения в обработанных деталях по сравнению со сваркой.
Рис. 9. Лазерная сварка металлических деталей
В заключение следует отметить, что лазерная наплавка выгодно отличается от традиционных методов обработки поверхности благодаря повышенной прочности соединения, качеству покрытия, гибкости процесса и меньшему воздействию на окружающую среду. Эти преимущества делают данный метод все более популярным выбором для различных применений в промышленности.
Сравнительная таблица
Таб. 1. Таблица сравнения лазерной наплавки с другими методами
Ответы на часто задаваемые вопросы
Существуют ли какие-либо проблемы с безопасностью при лазерной наплавке?
Лазерная наплавка предполагает использование мощных лазеров, которые могут представлять риск для безопасности, если ими не управлять должным образом. Операторы должны придерживаться строгих протоколов безопасности и использовать соответствующее защитное оборудование для предотвращения потенциальных опасностей, таких как повреждение глаз, ожоги или пожар.
Что такое разбавление при лазерной наплавке?
Разбавление при лазерной наплавке относится к смешиванию материала подложки (основного металла) с нанесенным наплавочным материалом в процессе плавления и затвердевания. Сильное разбавление может негативно повлиять на качество и свойства наплавленного слоя, такие как коррозионная стойкость, износостойкость и твердость. Одним из преимуществ лазерной наплавки является ее способность достигать низкого разбавления благодаря точному контролю тепла и малой зоне термического влияния, что обеспечивает высококачественное покрытие при минимальном смешивании материала подложки.
Можно ли выполнять лазерную наплавку чугуна?
Да, чугун можно плакировать лазером. Однако из-за хрупкости и высокого содержания углерода в чугуне необходимо соблюдать особую осторожность в процессе наплавки. Выбор материала для наплавки, предварительный нагрев чугунной подложки и точный контроль параметров процесса имеют решающее значение для минимизации растрескивания и успешной наплавки. В некоторых случаях для улучшения сцепления между чугуном и облицовочным материалом может использоваться переходный слой из другого материала.
Важна ли головка при лазерной наплавке?
Да, это важный компонент системы лазерной наплавки. Лазерная головка фокусирует лазерный луч на подложке, обеспечивая надлежащую плотность энергии и размер пятна для плавления и осаждения облицовочного материала. Лазерная головка также часто включает в себя сопло для подачи порошка. Конструкция, качество и точный контроль лазерной головки значительно влияют на общую производительность и результаты процесса лазерной наплавки.
Как выбираются материалы для лазерной наплавки?
Выбор материалов для наплавки зависит от желаемых свойств, требований к применению и совместимости с подложкой. При выборе подходящего материала для наплавки учитываются такие факторы, как износостойкость, коррозионная стойкость, твердость, тепловые свойства и стоимость. Кроме того, материал наплавки должен обладать хорошей совместимостью с подложкой для обеспечения надлежащего сцепления и минимизации дефектов. Обычные материалы, используемые при лазерной наплавке, включают нержавеющую сталь, сплавы на основе никеля, сплавы на основе кобальта и твердосплавные композиты. В некоторых случаях для достижения определенных эксплуатационных требований могут использоваться структуры из нескольких материалов.