Какие газы используются для лазерной резки и какие функции они выполняют
Какие газы используются для лазерной резки и какие функции они выполняют
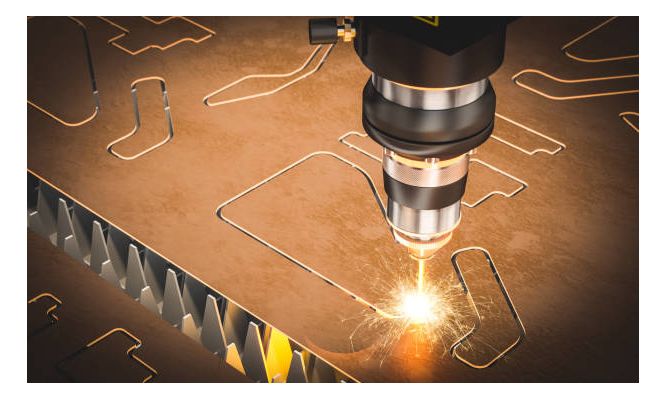
- Зачем нужен газ при лазерной резке?
- Виды газов для лазерной резки
- Лазерная резка с азотом
- Лазерная резка с кислородом
- Лазерная резка в атмосферном воздухе
- Недостатки воздуха для резки металла
- Лазерная резка с использованием инертных газов
- Факторы, влияющие на расход режущих газов
Для качественной резки и оптимальной производительности требуется не только сам металлорез, но и внимательное отношение к настройке параметров резки и грамотному выбору вспомогательного газа. В этой статье мы рассмотрим факторы, связанные с выбором газа для лазерной резки, и то, как это решение может повлиять на конечный результат.
Зачем нужен газ при лазерной резке?
Вспомогательные газы необходимы при лазерной резке по нескольким причинам.
Контроль тепла. Лазерная резка работает за счет интенсивного пучка сфокусированной энергии для испарения материала. Однако чрезмерный нагрев может привести к искажению материала и неровным краям реза, заусенцам. Вспомогательный газ необходим для контроля нагревания поверхности материала.
Вспомогательные газы, подаваемые через режущее сопло вместе с лазерным лучом, помогают управлять теплом и рассеивать его, тем самым предотвращая повреждение материала.
Газы способствуют удалению материала. Они создают поток, который эффективно удаляет расплавленный материал и остатки из зоны резки, обеспечивая чистоту и непрерывность резки. Лазерный резак расплавляет материал, а струя сжатого газа удаляет продукты горения.
Рис. 1. Лазерная резка металла
Безопасность. Режущие газы необходимы для безопасности, поскольку предотвращают воспламенение или искрение в тех случаях, когда процесс лазерной резки может представлять опасность.
Вспомогательный газ может повлиять на конечный продукт за счет:
- уменьшения температуры кромок разрезанного материала, предотвращения их деформацию;
- предотвращения образования опасных плазменных скоплений;
- защиты самого лазера от брызг и паров расплавленного металла;
- участие активного газа в экзотермическом процессе повышает скорость резки;
- защита кромки от контакта с окружающей средой при использовании инертного газа.
Рис. 2. Принцип работы лазерной резки
Виды газов для лазерной резки
Для удаления продуктов горения из зоны обработки для волоконных и CO2 лазеров через сопло подается вспомогательный газ. В качестве газа используются азот, кислород и воздух. В данном случае воздух также относится к газам.
Выбор вспомогательного газа для резки лазером зависит вида материала и его толщины.
Для лазерной резки используются данные вспомогательные газы:
- Активный — кислород;
- Воздух;
- Условно инертный — азот;
- Настоящие инертные газы — гелий и аргон.
Лазерная резка с азотом
Азот применяется в тех случаях, когда важно предотвратить окисление металла, что требует высокой концентрации азота для исключения негативного воздействия кислорода, а изменение цвета среза свидетельствует о низкой концентрации.
Азот является условно инертным газом. При резке с ним необходимо использовать более мощное лазерное оборудование. Для азота необходимо высокое сжатие и более глубокая фокусировка луча, что приводит к широким резам, и требует исключительной чистоты газа для сохранения антикоррозионных свойств стали.
Он также участвует в химических реакциях, однако является негорючим и не окисляет материал. Он не окисляет кромку в зоне резки, как это делает кислород или воздух. Именно реакций окисления и горения при работе с металлом стремятся избежать специалисты по изготовлению металлоконструкций. Азот после лазерного воздействия удаляет расплавленный материал из реза, оставляя металл в химически неизменном состоянии.
Азот подходит для резки:
- нержавеющей стали;
- высоколегированной стали;
- алюминия и его сплавов;
- латуни;
- черных металлов;
- никеля.
Рис. 3. Азот в баллоне
Азотная резка имеет множество преимуществ: кромки получаются чистыми, увеличивается сопротивление коррозии, нет перегрева и окалины, возможно качественно и долговечно окрасить обработанный металл.
Азот поставляется в газификаторах. Они представляют собой баллон, в котором азот находится в жидком состоянии. Газ в газификаторе чистый и занимает меньше места.
Лазерная резка с кислородом
Кислород обычно используется для резки низко- и среднелегированных стальных сплавов, за исключением участков, требующих нанесения краски на срезы, так как он вызывает реакцию окисления.
В лазерной резке использование кислорода в качестве вспомогательного газа используется для таких материалов, как:
- углеродистые стали;
- низколегированные стали;
- черные металлы.
Кислород выступает в роли окислителя и участвует в экзотермических реакциях. Вводя кислород в зону резки, усиливается тепловыделение, что делает процесс более быстрым и эффективным.
Однако важно отметить, что окислительная природа кислорода может привести и к окислению кромок реза. Если для черных и низколегированных сталей этот процесс можно контролировать, то для других материалов он становится более сложным, что приводит к окислению и ухудшению качества. Поэтому резка с кислородным сопровождением подходит для черных металлов, не обладающих нержавеющими или другими специальными свойствами.
Рис. 4. Кислород в баллоне
Лазерная резка в атмосферном воздухе
В качестве газовой среды вместо азота и кислорода может использоваться сжатый атмосферный воздух. Компрессор подает в лазерную магистраль его под нужным давлением, в результате чего воздух сжимается. Так как воздух почти на 80% состоит из азота, при попадании на металл он расплавляет его. Кислород, составляющий 20%, дает окислительную реакцию и дополнительно нагревает металл.
Рис. 5. Компрессор для сжатия воздуха
С помощью воздуха невозможно получить чистый и ровный срез для металлов толще 3 мм. Резка воздухом возможна для металлов небольшой толщины, около 1-1,5 мм.
Для резки тонких металлов достаточно компрессора с производительностью до 10 атмосфер. Воздушная резка применяется для:
- черного металла;
- нержавеющей стали;
- алюминия.
Недостатки воздуха для резки металла
Мнение о том, что лазерная резка металла с помощью воздуха - это дешевое и простое решение, обманчиво. Хотя кажется, что все, что вам нужно это единоразовая инвестиция в компрессор, на самом деле все гораздо сложнее. Лазерная резка металла с использованием воздуха влечет за собой скрытые расходы, которые часто застают производителей врасплох.
Во-первых, использование воздуха для лазерной резки требует значительных предварительных затрат. Помимо покупки компрессора, необходимо приобрести высококачественную систему фильтрации, стоимость которой может превосходить стоимость компрессора. Регулярное техническое обслуживание, включая замену масла в компрессоре, также увеличивает расходы. Фильтры в системе фильтрации также могут неожиданно выйти из строя, что приведет к нарушению процесса резки и потребует дополнительных мер для очистки.
Лазерная резка с использованием инертных газов
К инертным газам относятся гелий и аргон. Они не участвуют в окислительном процессе и не вступают в реакцию с полученным расплавом. По этой причине они выводят из зоны резки все газы, которые могли бы с ним реагировать.
Инертный газ можно использовать для резки титана, так как при резке с азотом образуются ненужные оксиды, которые негативно влияют на конечный результат.
Так как инертные газы стоят дороже азота, их используют редко, когда альтернативные варианты не подходят для конкретных материалов.
Факторы, влияющие на расход режущих газов
Тип газа: Металлообрабатывающие предприятия используют в основном азот и кислород, при этом требования к давлению газа составляют 8 бар для кислорода и до 20 бар для азота.
Чистота: Чистота определяется его концентрацией, при этом более высокие значения указывают на чистоту газа. В маркировке указывается количество "девяток" (X) и последняя цифра (Y), определяющая показатель чистоты.
Диаметр сопла: Широкое отверстие сопла требует большего количества газа для поддержания того же давления. Удвоение диаметра приводит к четырехкратному увеличению расхода.
Давление газа: Повышение давления улучшает качество резки, но одновременно увеличивает его расход. Оптимальный диапазон давления составляет 10-14 бар, хотя для конкретных задач его часто повышают до 15. Станки оснащены двумя газовыми соединениями: одно нерегулируемое для азота или воздуха, управляемое давлением, и второе для кислорода с прецизионным регулятором, позволяющим точно регулировать давление резки из программы.
Скорость резки: Скорость резки зависит от модели станка и влияет на расход газа. Низкая скорость резки требует больше времени на обработку и газа при раскрое листового металла.
Тип и толщина материала: На расход влияют толщина и тип материала. Более толстые заготовки и плотные материалы, такие как титан, требуют больше газа для обработки.
Мощность луча: Мощность лазерного луча влияет на скорость резки. Для толстых и прочных металлов предпочтительнее использовать более мощные лазерные устройства, так как они снижают расход газа и увеличивают скорость резки.
Настройки параметров: Различные настройки и регулировки станка также могут влиять на расход газа в зависимости от конкретных требований к обработке металла.