Виды лазерной резки. Технология и особенности режимов резки лазером
Виды лазерной резки. Технология и особенности режимов резки лазером
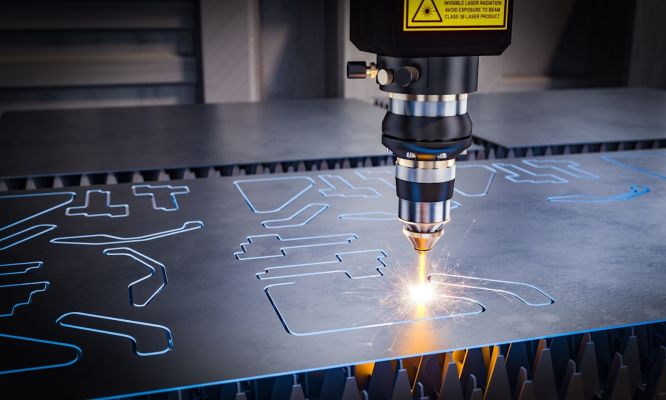
- Плюсы и минусы лазерной резки
- Виды лазерной резки
- Испарительная (сублимационная) резка
- Резка плавлением
- Реактивная плавящая резка (Кислородная резка)
- Резка с контролем разрушения
- Оборудование для лазерной резки
В связи с быстро растущим спросом на лазерную резку необходимо разрабатывать передовые технологии для повышения точности и экономичности данного процесса. Наиболее распространенными методами являются лазерная, плазменная, гидроабразивная и кислородная резка. По сравнению с другими технологиями, лазерная резка имеет преимущества в виде лучшей точности и аккуратности.
Станок лазерной резки - это автоматизированная система, состоящая из промышленного управляющего компьютера, серводвигателей, компьютерного числового управления и оптического датчика. Он состоит из механических и электрических частей управления. Оборудование для лазерной резки различается по источнику света, мощности и размерам. Известные варианты технологий лазерной резки включают в себя резку испарением, плавлением, реактивным плавлением и контролем разрушения материала.
От выбора режима резки зависит качество конечного результата - точность, ширина реза, четкость и шероховатость получаемых кромок, количество наплавленного металла (заусенцев), глубина реза. Но основное значение имеют такие параметры, как скорость резки и толщина обрабатываемого материала.
Плюсы и минусы лазерной резки
Плюсы лазерной резки
- Лазерная резка имеет большую скорость обработки материалов, чем другие традиционные способы резки, так как лазерное оборудование работает частично автоматизировано;
- При лазерной резке фиксация металлического изделия удобнее, чем при механической;
- Срезы, полученные с помощью лазера, более точные, чем при любом другом способе резки металлов. Именно по этой причине лазерная резка предпочтительна в тех отраслях, где требуется точный размер материала;
- В процессе лазерной резки металл не вступает в прямой контакт с другими материалами. Разные типы обработки лазером подходят для работы с заготовками различной конфигурации, особенно при использовании автоматизированных установок;
- Универсальность процесса позволяет гравировать тонкие рисунки на различных металлах;
- В случаях изготовления небольших партий продукции можно воспользоваться лазерной резкой, не прибегая к литью и штамповке.
Минусы лазерной резки
- Лазерная резка требует большого потребления энергии по сравнению с другими методами; Лазерный луч требует тщательной и точной настройки;
- Малейшая ошибка при регулировке расстояния и температуры может привести к выгоранию или обесцвечиванию металла;
- Лазерный луч может нанести вред здоровью при неправильной эксплуатации;
- Лазерная резка подходит не для всех типов металлов.
Виды лазерной резки
Испарительная (сублимационная) резка
Резка испарением применяется наиболее часто благодаря высокой мощности лазерного излучения, которая позволяет поверхности заготовки быстро достичь нужной температуры. При лазерной резке испарением лазерный луч работает в импульсном режиме. Как только лазерное облучение попадает на механическую заготовку, оно эффективно поглощается и преобразуется в тепловую энергию. Попадая на поверхность заготовки быстро достигается температура плавления. Чтобы пары материала не конденсировались на стенках кромки, толщина материала не должна превышать диаметр лазерного луча.
Резка испарением не применяется для таких материалов, как дерево и некоторые виды керамики, которые не имеют расплавленного состояния и поэтому менее склонны к образованию конденсата.
Под действием окисления поверхности скорость поглощения значительно улучшается, а выбрасываемый пар сдувает большое количество расплавленного материала, способствуя его испарению в выемку. Лазерная резка испарением часто используется для резки очень тонких металлических и неметаллических материалов.
Рис. 1. Технология лазерной резки
Резка плавлением
Резка оплавлением требует такой мощности лазера, чтобы он мог резать и обрабатывать поверхность заготовки для формирования связки. В отличие от паровой резки, расплав в условиях резки плавлением должен быть продут вспомогательным газом, а не удален в процессе газификации. Расплавленный материал удаляется потоком воздуха. Резка плавлением позволяет избежать проблемы испускания и поглощения лазерного луча паром. Когда лазерный луч движется в зазоре надреза, он взаимодействует только с передним материалом. Угол выстрела слишком велик, когда лазерный луч проецируется на поверхность материала заготовки, поглощенная лазерная энергия не может продолжать плавиться. Поэтому процесс плавления должен выполняться поэтапно. Мощность лазера, используемого при резке плавлением, намного меньше, чем при резке испарением. В основном она применяется для материалов, которые могут экзотермически реагировать с кислородом, таких как обычный алюминий и медь. В качестве вспомогательных газов используются различные инертные и неактивные газы. Преимуществом лазерной резки с оплавлением является получение практически неоксидной режущей кромки.
При резке в инертном газе чаще всего рабочей средой является инертный газ азот, для резки титана используют аргон.
Она используется в тех случаях, когда заготовки должны отвечать высоким визуальным требованиям без дальнейшей обработки. Когда расплав выбрасывается из пропила под действием вспомогательного газа, часть его может прилипнуть к нижней кромке реза и образовать заусенец. Регулировка параметров процесса для минимизации образования заусенцев является сложной задачей, которая становится все более трудной по мере увеличения толщины листа. Выброс расплава, образующий компактный и стабильный трехкратный поток, является характерным свойством реза без заусенцев.
Рис. 2. Процесс лазерной резки металла
Реактивная плавящая резка (Кислородная резка)
Суть реактивной плавильной резки заключается в эффективном нагреве заготовки до точки воспламенения с помощью лазерного луча, после чего происходит экзотермическая реакция на основе промышленного чистого кислорода. Во время этого процесса выделяется большое количество тепла. Материал в месте надреза окисляется и сгорает, образуя расплавленный оксид, который разлетается и образует надрез. В то же время выделяющееся тепло может быть подведено к соседним материалам для достижения точки воспламенения. Таким образом, можно обеспечить непрерывное реактивное плавление и резку.
Кислородная лазерная резка делается с меньшей скоростью, обычно составляющей порядка 0,2 м/мин. Использование лазерного оборудования мощностью 6 кВт позволяет разрезать металлы толщиной до 100 мм.
Мощность лазера, необходимая для реактивной резки плавлением, составляет менее 1/20 мощности лазера для резки испарением. Он широко используется для резки стали и титановых материалов на машиностроительных предприятиях. Однако большое количество экзотермической энергии, выделяемой при окислении материала, дестабилизирует фронт расплава, и сильно окисленная кромка реза получается с большой шириной прожога.
Резка с контролем разрушения
Высокоскоростная и контролируемая резка с нагреванием лазерным лучом применяется для обработки хрупких материалов, которые подвержены термическому повреждению.
Суть данного процесса резки заключается в следующем:
Лазерный луч нагревает маленький фрагмент хрупкого материала, создавая большой тепловой градиент и резкую механическую деформацию в этой области, что провоцирует разрушение материала. При сохранении сбалансированного градиента нагрева лазерный луч воздействует в заданном направлении.
Оборудование для лазерной резки
Современные многокоординатные станки приходят на смену шумным и не очень производительным механическим станкам. На производительность лазерного оборудования оказывает влияние специфика производства и экономическая оправданность тех или иных устройств. С использованием новейшего лазерного оборудования с ЧПУ можно резать заготовки из различных видов металла с погрешностями, не превышающими 0,005 мм.
Некоторые модели позволяют резать изделия площадью до нескольких квадратных метров. При этом персонал по минимуму задействован в автоматизированном техпроцессе обработки. Чертежи необходимых деталей загружаются в ПО оборудования, далее программа регулирует как лазерный луч, так и рабочий стол, на который помещаются заготовки.
С помощью систем автофокусной настройки устройство подбирает оптимальное расстояние, требуемое для эффективной обработки. Температура оборудования контролируется с помощью специальных теплообменников, оператору станка передаются контрольные данные, относящиеся к текущему состоянию инструмента. В станках установлены клапанные механизмы, обеспечивающие подсоединение газового оборудования, посредством которого в рабочую зону поступают вспомогательные газы.
Статьи по данной теме: Лазерная резка металла, Лазерная резка алюминия, алюминиевых пластин