Почему лазерный станок плохо режет — причины и настройка станка
Почему лазерный станок плохо режет — причины и настройка станка
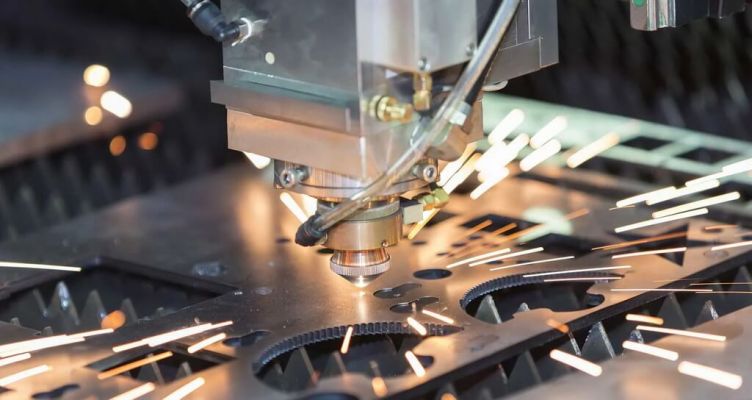
- Причины, по которым лазер не может разрезать металл
- Решение проблемы, когда лазер не режет
- Дефекты лазерной резки металла
- Устранение неточности реза на лазерном станке с ЧПУ
- Техническое обслуживание волоконного лазера
Лазерная резка является популярным методом, используемым в различных отраслях промышленности для разрезания материалов с высокой точностью. Однако бывают случаи, когда лазер может столкнуться с трудностями при обработке металла. В этой статье мы рассмотрим причины этой проблемы и предложим практические решения для обеспечения оптимальной производительности лазерной обработки.
Причины, по которым лазер не может разрезать металл
Недостаточная мощность: Одна из основных причин почему лазерный станок для резки не может прорезать материал. Если мощность лазера недостаточна для толщины или типа обрабатываемой заготовки, то результат будет неудовлетворительным.
Неправильное выравнивание фокуса: Лазерная резка требует точного выравнивания фокуса для обеспечения чистого и эффективного реза. Если лазерный луч неправильно сфокусирован это может привести к снижению производительности резки или полной невозможности прорезать металл. Если световой путь неправильный, его необходимо отрегулировать и настроить фокусное расстояние, пока лазер не сделает круглую отметку на бумаге.
Отражающие поверхности: Металлы с отражающей поверхностью, такие как алюминий или медь, могут вызвать проблемы при лазерной резке. Лазерный луч отражается от поверхности вместо того, чтобы поглощаться, что приводит к снижению производительности резки.
Твердость материала: Различные металлы обладают разной степенью твердости, что может быть причиной неэффективной обработки. Более твердые материалы, такие как нержавеющая сталь или титан, могут потребовать большей мощности лазера или меньшей скорости резки для достижения успешного реза. Регулировка параметров резки в соответствии с конкретной твердостью металла может помочь преодолеть эту проблему.
Рис. 1. Схема прохождения лазерного луча
Состав материала: Некоторые металлы имеют состав сплава, который делает их более сложными резки лазером. Например, некоторые сплавы с высоким содержанием таких элементов, как никель или хром, могут иметь плохие свойства поглощения, что снижает эффективность резки. Анализ состава разрезаемого металла и соответствующая юстировка станка помогут оптимизировать эффективность.
Толщина материала: Возможности лазерной резки ограничены толщиной металла. Если материал слишком толстый для используемой мощности, он может не справиться с проникновением и завершением резки. Для толстых материалов подходят альтернативные методы резки, такие как фрезерование или использование более мощных лазеров.
Качество луча: Качество лазерного луча также может повлиять на производительность. Если луч плохо сфокусирован это может привести к плохому качеству резки. Регулярное техническое обслуживание и калибровка лазерной системы, включая проверку оптики и компонентов доставки луча, помогут обеспечить оптимальное качество луча.
Ограничения станка: Различные станки для лазерной резки имеют определенные возможности и ограничения. Важно учитывать, подходит ли используемый станок для предполагаемых задач. Для преодоления ограничений и достижения желаемых результатов может потребоваться модернизация до более мощного или специализированного лазерного станка.
Падение мощности: Для решения проблемы, когда мощность лазера падает, а ток мал, необходимо вовремя заменить лазерную трубку и использовать более мощный регулятор напряжения.
Рис. 2. Резка металлических материалов излучением непрерывного СО2 лазера
Решение проблемы, когда лазер не режет
Проверить мощность лазера: важно убедиться, что мощность лазера установлена правильно для конкретного металла и толщины резки. Обратитесь к руководству по эксплуатации лазерной системы или свяжитесь с производителем для получения рекомендаций по настройкам мощности.
Проверяйте выравнивание фокуса: Регулярно проверяйте и выравнивайте фокус лазерного луча, чтобы гарантировать точную и аккуратную резку. Правильное выравнивание фокуса повышает способность лазера эффективно проникать в металл и резать его.
Оптимизация параметров резки: Настройка параметров резки может существенно повлиять на способность лазера резать металл. Такие параметры, как скорость резки, плотность мощности и давление вспомогательного газа, могут быть точно настроены для повышения производительности. Экспериментирование с различными настройками может привести к улучшению результатов. Вспомогательный газ используется для того, чтобы помочь удалить расплав из зоны резки. Когда давление воздуха не недостаточно высоко, расплав трудно удалить, что приводит к не прорезания металла.
Повышение мощности лазера: Если мощности лазера недостаточно для резки более толстых или твердых металлов необходимо перейти на лазерную систему с более высокой мощностью. Проконсультируйтесь с производителями или поставщиками лазерных станков, чтобы изучить варианты, которые лучше соответствуют вашим требованиям к резке.
Внедряйте технику прожига: В некоторых случаях лазеру трудно начать процесс резки из-за толщины или состава металла. Применение методов предварительного сверления отверстий или использование импульсного прошивания, может помочь создать точку входа лазерного луча, способствуя плавной и непрерывной резке.
Учитывайте подготовку материала: Обеспечение надлежащей подготовки материала может способствовать успешной лазерной резке. Очистка поверхности металла от масел, ржавчины или покрытий помогает улучшить поглощение лазера и предотвратить помехи во время резки. Кроме того, использование зажимов или приспособлений для фиксации материала на месте снижает вибрации и повышает точность резки.
Минимизация отражения: При работе с металлами с высокой отражательной способностью следует применять антиотражательные меры для минимизации отражения луча. Они могут включать использование специализированных покрытий на поверхности металла или настройку параметров лазера для оптимизации производительности резки.
Дефекты лазерной резки металла
Лазерная резка металла, хотя и является высокоточным и эффективным процессом, может иметь определенные дефекты, которые влияют на ее качество. Вот некоторые распространенные дефекты и их возможные причины:
Изменение ширины пропила
Пропил относится к ширине разреза, сделанного лазером. Несоответствующая ширина пропила может привести к неровным краям и нарушению точности размеров. Причинами изменения ширины пропила могут быть колебания мощности лазера, непостоянная скорость подачи материала или неправильное выравнивание фокуса.
При правильных настройках оборудования и внимательности оператора вероятность брака на выходе практически нулевая.
Тепловое искажение
Лазерная резка связана с выделением интенсивного тепла, которое может вызвать тепловые искажения на обработанном металле. Это искажение может привести к короблению или изгибу материала. Высокая мощность лазера, неправильные параметры резки или недостаточное охлаждение могут способствовать возникновению термических искажений.
Рис. 3. Искривления стальных листов (коробление) а — местные выпуклости; б — волнистость по длине.
Заусенцы и шлак
Заусенцы - это нежелательные выступы или неровные края, которые образуются вдоль линии реза, а шлак - это расплавленный или затвердевший материал, который прилипает к нижней части реза. Эти дефекты могут возникать из-за таких факторов, как чрезмерная мощность лазера, недостаточный поток вспомогательного газа или неправильное выравнивание фокуса. Они могут негативно повлиять на качество и внешний вид разреза.
Рис. 4. Заусенцы на металле (грат)
Конический рез
Конический рез имеет различные углы или толщину по всей длине. Этот дефект может возникнуть из-за нескольких факторов, включая непостоянную подачу луча, неправильное выравнивание фокуса или неравномерные свойства материала. Достижение параллельного и равномерного среза может быть сложной задачей, особенно для толстых материалов.
Рис. 5. Юстировка лазерного резака
Надрезы
Дефекты надреза или подреза связаны с образованием нежелательной канавки или углубления на кромке реза. Эти дефекты могут возникать из-за чрезмерной мощности лазера, неправильного выравнивания фокуса или недостаточного потока вспомогательного газа. Они могут нарушить структурную целостность отрезанной детали и помешать ее функциональности.
Точная настройка мощности лазера, обеспечение последовательного выравнивания фокуса, оптимизация потока вспомогательного газа и меры по охлаждению являются важнейшими шагами для минимизации дефектов и достижения высококачественных результатов лазерной резки металла.
Регулярное техническое обслуживание не только обеспечивает постоянную производительность, но и помогает выявить потенциальные проблемы до того, как они перерастут в серьезные проблемы. Рекомендуется вести журнал технического обслуживания для отслеживания выполняемых задач, графиков и любых замеченных проблем.
Рис. 6. Последствия неправильной настройки лазерного станка
Устранение неточности реза на лазерном станке с ЧПУ
- Проверьте выравнивание материала: Убедитесь в правильном выравнивании и точном расположении материала на рабочем столе;
- Проверьте параметры резки: Подтвердите запрограммированные параметры, включая скорость подачи, мощность лазера, положение фокуса и давление вспомогательного газа;
- Постоянно очищайте сопло от инородных примесей, увеличивайте давление вспомогательного газа до требуемого уровня и вовремя заменяйте дистиллированную воду в системе охлаждения;
- Настройте оптику и подачу луча: Важен осмотр состояния лазерной оптики, при необходимости очистите или замените компоненты;
- Выравнивание лазерного луча: Убедитесь в правильном выравнивании лазерного луча относительно режущей головки и всего станка;
- Оцените свойства материала: Учитывайте твердость, состав и толщину материала при настройке параметров резки;
- Калибровка станка: Регулярно калибруйте лазерный станок с ЧПУ для поддержания точности;
- Проводите пробные разрезы и корректировать: Выполняйте пробные резы, анализируйте результаты и вносите итерационные корректировки для достижения желаемой точности.
Техническое обслуживание волоконного лазера
Техническое обслуживание волоконного станка включает в себя регулярные проверки, чистку и обслуживание для обеспечения оптимальной производительности и долговечности. Вот некоторые общие задачи по обслуживанию станка для волоконного лазера:
Ежедневное обслуживание
- Проверьте систему охлаждения. Убедитесь, что уровень охлаждающей жидкости достаточен, а температура находится в рекомендуемом диапазоне. При необходимости очистите или замените фильтры охлаждающей жидкости.
- Проверьте источник питания. Убедитесь, что блок питания функционирует должным образом и нет ослабленных соединений или поврежденных кабелей.
- Очистите внешнюю поверхность. Протрите внешние поверхности машины, чтобы удалить пыль и мусор. Используйте чистую безворсовую ткань или соответствующий чистящий раствор.
Еженедельное обслуживание
- Очистите рабочую зону. Удалите любой мусор или лишние материалы из рабочей зоны, включая режущую станину и окружающие компоненты.
- Осмотрите зеркала и линзы. Проверьте состояние зеркал и линз на наличие загрязнений, пятен или повреждений. На поверхности линз появляется нагар, что снижает мощность лазерного оборудования. Аккуратно очистите их с помощью безворсовых тампонов и раствора для очистки линз.
- Применяйте пылесос чтобы убрать пыль и грязь в резаке раз в неделю, а все электрические шкафы должны быть закрыты для защиты от пыли.
Ежемесячное техническое обслуживание
- Выполните проверку выравнивания. Проверьте соосность лазерного луча с системой подачи и другими оптическими компонентами. При необходимости выполните регулировку.
- Очистите лазерный источник. В зависимости от типа волоконного лазера, лазерный источник может нуждаться в периодической очистке. Следуйте инструкциям производителя.
- Осмотрите систему охлаждения. Осмотрите систему охлаждения на предмет утечек, засоров или нарушений. Очистите или замените фильтры и обеспечьте надлежащую циркуляцию охлаждающей жидкости.