Фильтры
Описание технологии лазерной закалки
Лазерная закалка (термоупрочнение) — это метод локального термического упрочнения, при котором поверхность металла быстро нагревается фокусированным лазерным лучом, а затем самозакаляется.
Цель — повысить износостойкость и долговечность деталей, увеличить их устойчивость к трению, коррозии, влажности и другим факторам.
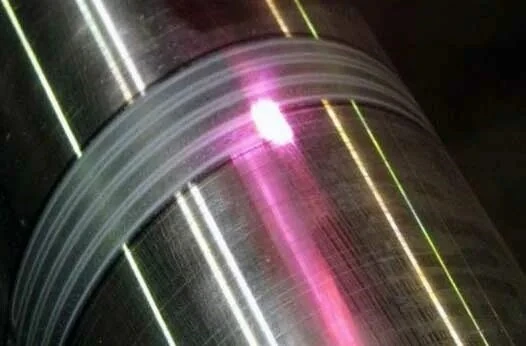
Лазерный луч (обычно CO2 или оптоволоконный лазер) мгновенно облучает поверхность материала высокой плотностью энергии (10³~10⁶ Вт/см²), в результате чего чрезвычайно тонкая поверхность (0,1–2 мм) нагревается до температуры аустенизации. Это процесс термической обработки стали, который превращает её структуру в аустенит путем доведения до критических температур за чрезвычайно короткое время (миллисекунды).
Тепло быстро рассеивается через основной материал со скоростью охлаждения до 10³-10⁶ ℃/сек., образуя мартенсит (сталь) или аморфную/нанокристаллическую структуру (некоторые сплавы), значительно повышая твердость поверхности.
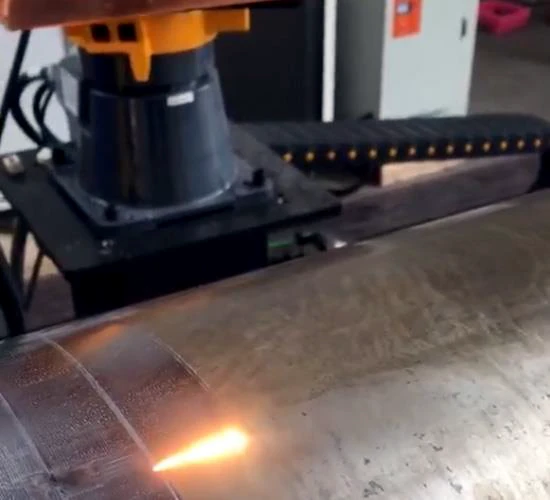
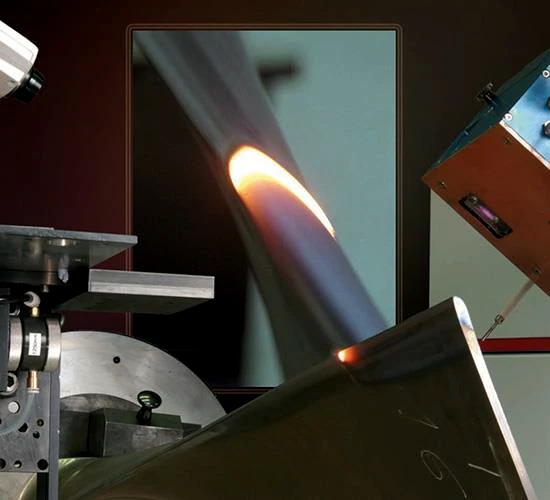
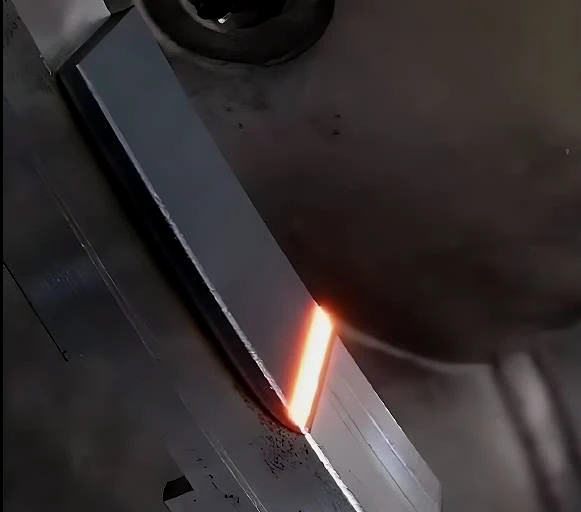
Видео работы станков
Основные принципы технологии
Процесс лазерной закалки включает несколько этапов:
- Фокусировка лазерного луча на поверхности детали с помощью зеркал и линз
- Нагрев металла до температуры аустенитного превращения (обычно выше 850°C). Рисунок 1
- Перемещение луча и нагрев следующей зоны обработки
- Быстрое охлаждение нагретого слоя за счёт теплопроводности. В результате на поверхности образуется закалённый слой (мартенсит), который превосходит по прочности исходный материал. Глубина закалённой области — 0,1–3 мм. Рисунок 2
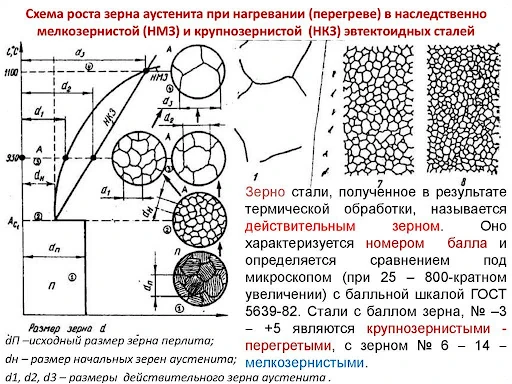
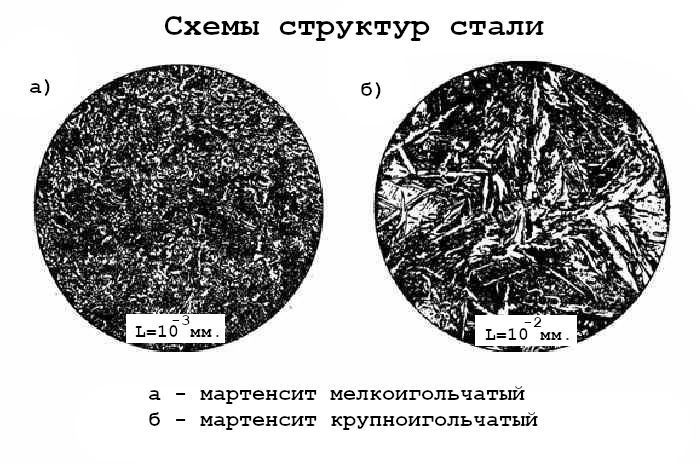
Лазерная закалка обеспечивает высокую плотность изделий и быстрое охлаждение, не требуя охлаждающей среды, такой как вода или масло. По сравнению с индукционной и пламенной технологиями закалки, или процессом цементации, - лазерная закалка обеспечивает однородность упрочняемого слоя, его более высокую твердость, малую деформацию заготовки.
При этом, глубину закаляемого слоя и траекторию нагрева легко контролировать, легко автоматизировать, не нужно проектировать соответствующую индукцию катушки в зависимости от размера детали. Например, для обработки крупных деталей, нет необходимости ограничивать размер камеры печи, в случае химико-термической обработки, такой как цементация.
Поэтому во многих отраслях промышленности процесс лазерной закалки постепенно заменяет традиционные процессы. Особенно важно то, что деформация заготовки до и после лазерной закалки очень незначительна, что особенно подходит для обработки поверхности деталей с высокими требованиями к точности.
Преимущества технологии
Эта современная технология по праву занимает место традиционных процессов, ознакомьтесь со всеми преимуществами:
- Лазерная закалка гарантирует малую деформация заготовки. За счёт локального нагрева не возникает значительных напряжений, что особенно хорошо подходит для поверхностной обработки высокопрочных и сложных деталей
- Обеспечивает высокую плотность и быструю скорость охлаждения, без необходимости использования охлаждающего устройства.
- По сравнению с индукционной закалкой, пламенной закалкой, закалкой цементацией, - лазерная гарантирует однородность упрочненного слоя и его более высокую твердость. Параметры контроля температуры можно регулировать в режиме реального времени для обеспечения максимального качества обработки.
- Глубина нагреваемого слоя и траектория нагрева легко поддаются измерению и управлению. Это позволяет легко автоматизировать весь процесс
- Не нужно проектировать соответствующие размеру различных деталей индукционные катушки или ограничивать размер камеры печи для химико-термической обработки
- Детально легко и точно позиционируется на станке с ЧПУ для локальной, канавочной и щелевой закалки
- Лазерная закалка потребляет мало энергии, является чистой и эффективной технологией. Не требует использования дополнительных ресурсов
Сравнение с традиционными методами
Процесс | Плюсы | Минусы |
Лазерная закалка | Малая деформация, селективное упрочнение, контролируемая глубина слоя, автоматизированная обработка, повышенная твердость, износостойкость | Глубина закалки ограничена, обычно, в пределах 1,5 мм. Относительно дорогое оборудование |
Индукционная закалка | Быстрая обработка, большая глубина слоя, более дешевое оборудование, широко используемая сейчас технология | Требуется закалочная среда, большая деформация деталей, легко переплавить поверхности |
Пламенная закалка | Дешевая и гибкая мобильная обработка | Интенсивность ручного труда, загрязнение окружающей среды, неравномерность упрочняющего слоя, деформация деталей, закалка легко поддается трещинам |
Электро-закалка (ТВЧ) | Низкая деформация, глубокий закалочный слой, не требуется закалочная среда | Дорогостоящее оборудование, вакуумная среда, низкая эффективность обработки, крупные детали не могут быть обработаны |
Основной недостаток лазерной закалки - высокая стоимость оборудования. Поэтому мы стараемся сделать ее доступной нашим клиентам, предлагая станки марки TORWATT - максимально надежные и сбалансированные по цене.
Также стоит отметить необходимость очистки поверхности от ржавчины и окалины перед закалкой. Для решения этой задачи, мы предлагаем ознакомиться с оборудованием лазерной очистки нашего каталога.
Примеры использования
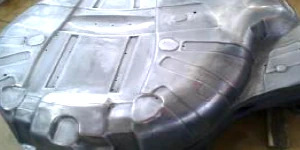
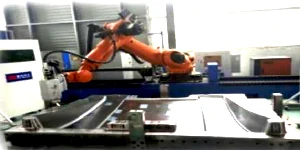
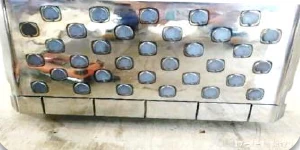
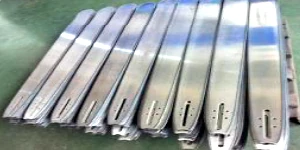
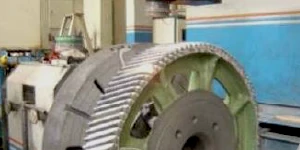
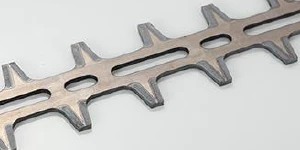