Лазерная закалка металла: Современная технология обработки поверхности для улучшения характеристик деталей
Лазерная закалка металла: Современная технология обработки поверхности для улучшения характеристик деталей
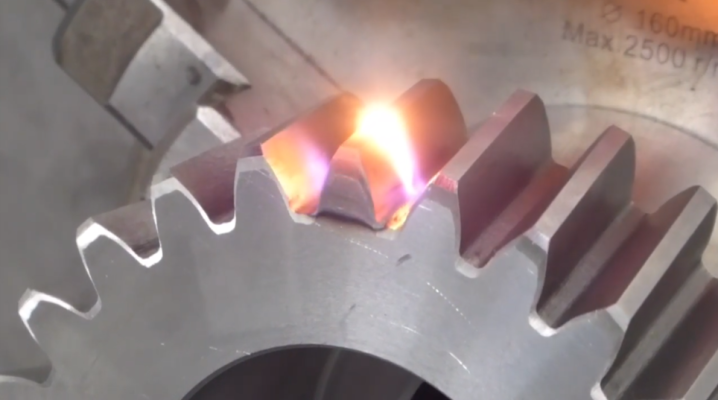
- Что такое лазерная закалка?
- Принцип работы устройств лазерной термообработки
- Области применения лазерной закалки
- Автомобильная промышленность
- Аэрокосмическая промышленность
- Инструментальная и штамповочная промышленность
- Производство тяжелых машин и оборудования
- Преимущества лазерной закалки
- Ограничения и проблемы
- Часто задаваемые вопросы
Что такое лазерная закалка?
Лазерная закалка, также известная как лазерная термообработка - это современная технология упрочнения поверхности, используемая для повышения износостойкости и долговечности металлических деталей. Процесс включает в себя использование сфокусированного лазерного луча для быстрого нагрева определенного участка поверхности материала. Высокоэнергетический лазер нагревает поверхностный слой, вызывая изменение микроструктуры материала, увеличивая его сопротивляемость к трению, коррозии, влажности и другим внешним факторам.
Более того, универсальность лазерной технологии выходит за рамки закалки, поскольку она также широко применяется для резки, маркировки и пайки. В результате лазерная технология продолжает вносить радикальные изменения в производственную отрасль, предлагая инновационные решения для обработки металлов и повышая общую эффективность и устойчивость этих операций.
Принцип работы устройств лазерной термообработки
Рис. 1. Принцип работы лазерной термообработки
Генерация лазерного луча: Лазерный источник CO2 или волоконного лазера , генерирует высокоэнергетический лазерный луч, который можно точно контролировать и направлять.
Фокусировка лазерного луча: Лазерный луч фокусируется на поверхности металлической детали с помощью линзы или других оптических систем. Фокусировка обеспечивает концентрацию энергии в нужной области, обеспечивая точную и целенаправленную закалку.
Быстрый нагрев: Сфокусированный лазерный луч быстро нагревает поверхностный слой металла, обычно в течение миллисекунд, повышая температуру материала до температуры аустенитизации, при которой его микроструктура превращается из ферритной или перлитной фазы в аустенитную. Большая температура изменяет расположение атомов углерода в структуре металла, после чего начинается аустенитное превращение.
Рис. 2. Лазерное термоупрочнение
Фазовое превращение: По мере перемещения лазерного луча нагретая область быстро охлаждается благодаря теплопроводности материала, в результате чего аустенитная фаза превращается в твердую, износостойкую мартенситную фазу. Такое быстрое охлаждение известно как самозакалка, и оно устраняет необходимость во внешних закалочных средствах.
Контролируемая закалка: Регулируя такие параметры, как мощность лазера, скорость сканирования и перекрытие луча, можно точно контролировать процесс закалки для достижения желаемой твердости, глубины и однородности. Процесс может использоваться для локальной закалки определенных участков детали или для обработки всей поверхности.
Благодаря закалке на поверхности образуется высокодисперсный мартенсит (игольчатые зерна, в которых находится сверхнасыщенный твердый раствор углерода в альфа-железе), в результате чего прочность материала значительно возрастает.
Отличия лазерной закалки от традиционных методов
Лазерная закалка и традиционные методы закалки отличаются по различным аспектам, включая процесс, точность, воздействие на окружающую среду и результаты.
Процесс: Лазерная закалка использует высокоэнергетический лазерный луч для быстрого нагрева быстро изнашиваемой поверхности. Традиционные методы, такие как индукционная или пламенная закалка работают с помощью электрического тока или открытого пламени, с последующей закалкой в жидкой среде.
Точность: Лазерная закалка обеспечивает большую точность, позволяя целенаправленно закаливать определенные участки без воздействия на окружающий материал. Традиционные методы часто приводят к увеличению зоны термического влияния, что может привести к деформации или нежелательным изменениям свойств материала.
Скорость: Лазерная закалка - это быстрый процесс, нагрев и охлаждение происходят в течение миллисекунд. Традиционные методы обычно требуют более длительного времени нагрева и охлаждения, что может привести к увеличению потребления энергии и времени производства.
Глубина закалки: Лазерная закалка проникает неглубоко, от микрометров до нескольких миллиметров. Традиционные методы, такие как науглероживание или азотирование, позволяют достичь более глубокой закалки.
Бесконтактность: Лазерная закалка - это бесконтактный процесс, снижающий риск загрязнения и деформации. Традиционные методы закалки могут включать физический контакт между источником тепла и деталью, что потенциально может привести к деформации материала.
Рис. 3. Лазерное закаливание металла
Области применения лазерной закалки
Лазерная закалка применяется во многих отраслях промышленности для обработки таких материалов, как:
- цилиндрические детали – валы, кольца, втулки;
- режущие кромки ножей;
- медицинские инструменты;
- чугун с шаровидным и пластинчатым графитом;
- резьбовые поверхности насосно-компрессорных труб;
- штампы, ударопрочные подшипники.
Автомобильная промышленность
Автомобильная промышленность получает огромную пользу от лазерной закалки, поскольку она используется для обработки таких важных компонентов, как детали двигателя, шестерни и валы. Такая обработка помогает повысить износостойкость и продлить срок службы этих компонентов, улучшая эксплуатационные характеристики и надежность автомобиля.
Аэрокосмическая промышленность
В аэрокосмической отрасли лазерная закалка используется для обработки лопаток турбин, деталей шасси и других деталей, подверженных экстремальным условиям и износу. Повышая твердость поверхности и износостойкость этих компонентов, лазерная закалка помогает повысить их долговечность и безопасность.
Инструментальная и штамповочная промышленность
Инструментальная и штамповочная промышленность использует лазерную закалку для повышения производительности и долговечности режущих инструментов, пуансонов, штампов и пресс-форм. Инструменты, упрочненные лазером, имеют повышенную устойчивость к износу и деформации.
Производство тяжелых машин и оборудования
Производители тяжелых машин и оборудования используют лазерную закалку для обработки таких компонентов, как подшипники, шестерни и гидравлические цилиндры. Обработка помогает увеличить долговечность и производительность этих компонентов, снижая затраты на техническое обслуживание и время простоя.
Преимущества лазерной закалки
Точность и контроль
Одним из значительных преимуществ лазерной закалки является высокий уровень точности. Процесс позволяет обрабатывать определенные участки детали, не затрагивая окружающий материал. Такая точность позволяет производителям выборочно обрабатывать участки, улучшая эксплуатационные характеристики деталей и сводя к минимуму риск изменений свойств материала.
Экологически безопасно
По сравнению с традиционными методами закалки, лазерная более экологична. Процесс требует меньше энергии и производит меньше выбросов. Снижается общий углеродный след производственного процесса, что делает его более экологичным.
Минимальное обслуживание и более длительный срок службы
Компоненты, обработанные с помощью лазерной закалки, часто требуют меньшего обслуживания и имеют более длительный срок службы по сравнению с компонентами, обработанными традиционными методами закалки. Повышенная износостойкость и уменьшение деформации в результате лазерной закалки способствуют снижению затрат на техническое обслуживание и времени простоя, что в конечном итоге повышает общую эффективность работы.
Адаптируемость и интеграция
Лазерная закалка отличается высокой адаптивностью и может быть легко интегрирована в существующие производственные линии, это снижает потребность в дополнительных площадях и оборудовании. Процесс может быть включен в различные этапы производства, от предварительной обработки до окончательной отделки, и может применяться к широкому спектру материалов и компонентов. Такая адаптивность позволяет производителям оптимизировать свои производственные процессы и повысить качество продукции.
Равномерная глубина закалки
Лазерная закалка обеспечивает равномерную глубину закалки по всей обрабатываемой поверхности. Вся обработанная область дает улучшенные характеристики износостойкости и твердости.
Сниженный риск загрязнения
Так как лазерная закалка является бесконтактным процессом, снижается риск загрязнения маслами, закалочными составами и другими веществами, используемыми при традиционных методах закалки. Снижение риска загрязнения помогает сохранить целостность и чистоту обработанных компонентов, улучшая общее качество и производительность.
Рис. 4. Способы лазерной закалки
Ограничения лазерной закалки
Пригодность материала
Не все материалы подходят для лазерной закалки. Процесс наиболее эффективен для материалов с высокой скоростью поглощения и достаточной температурой превращения. Некоторые материалы, особенно цветные металлы или материалы с низким коэффициентом поглощения, могут плохо реагировать на лазерную закалку.
Первоначальные инвестиции и затраты на установку
Оборудование для лазерной закалки может быть дорогим, причем первоначальные инвестиции могут быть выше, чем у традиционного закалочного оборудования. Кроме того, для настройки и интеграции систем лазерной закалки в существующие производственные линии могут потребоваться специальные знания и дополнительные ресурсы.
Сложность процесса
Точный контроль параметров лазера, таких как мощность, скорость сканирования и перекрытие луча, имеет решающее значение для достижения желаемых результатов закалки. Для эффективной работы необходимы квалифицированные операторы и современные систем мониторинга процесса.
Зона термического влияния
Лазерная закалка уменьшает зоны термического влияния по сравнению с традиционными методами, но все же существует риск микроструктурных изменений или нежелательного влияния на свойства материала. Тщательный контроль параметров лазера необходим для минимизации этих рисков.
Рис. 5. Процесс лазерной закалки металлических изделий
Ограниченная глубина закалки
Закалка может составлять от нескольких микрометров до нескольких миллиметров. Этого может быть недостаточно для определенных применений, требующих глубокой закалки корпуса. Для достижения требуемой глубины могут потребоваться альтернативные методы, такие как науглероживание или азотирование.
Риск перегрева и прожига
Из-за быстрого нагрева при лазерной закалке существует риск перегрева, если параметры лазера не контролируются должным образом. Это может привести к повреждению детали и снижению производительности.
Ограничения по размеру
Лазерная закалка лучше всего подходит для деталей малого и среднего размера или локальной закалки определенных участков. Процесс может быть менее эффективным или более трудоемким для крупногабаритных деталей.
Неравномерное упрочнение поверхности
В некоторых случаях процесс лазерной закалки может привести к неравномерному упрочнению по всей обрабатываемой поверхности. Это может быть вызвано изменением поглощающих свойств материала или несоответствием траектории сканирования лазерного луча.
Рис. 6. Станок для лазерной закалки обрабатывает металлическую деталь
Часто задаваемые вопросы
Какова основная цель лазерной закалки?
Основная цель лазерной закалки - повышение поверхностной твердости и износостойкости металлов и сплавов, улучшение их долговечности и эксплуатационных характеристик.
Чем лазерная закалка отличается от обычных методов закалки?
Лазерная закалка - это бесконтактный, точный и контролируемый процесс, который уменьшает искажения и остаточное напряжение по сравнению с традиционными методами закалки, которые опираются на прямой контакт или проводимость.
Подходит ли лазерная закалка для всех типов металлов и сплавов?
Хотя лазерная закалка эффективна для многих типов металлов и сплавов, она может не подходить для материалов с низкой скоростью поглощения или низкой температурой превращения. Эффективность лазерной закалки зависит от конкретного материала и его свойств.
В каких отраслях промышленности лазерная закалка приносит наибольшую пользу?
Лазерная закалка выгодна для нескольких отраслей промышленности, включая автомобильную, аэрокосмическую, инструментальную и штамповочную, а также производство тяжелого машиностроения.
Наша компания подробно изучила этот тип оборудования и может предложить клиентам полноценно интегрировать его в деятельность своих предприятий.
Ознакомьтесь с доступным ассортиментом оборудования на странице каталога
станков лазерной закалки.